
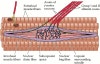
Clock a precision dowel in the toolholder to see the toolholder’s runout.ģ. Clock the inside of the spindle taper to see the spindle’s runout.Ģ. The measurement shown will get you runout from all sources, but it’s important to understand that you may want to measure the individual component sources of spindle-tool runout to find the underlying causes.ġ. Photo and description of measurement courtesy of Given a dial test indicator and a magnetic holder, it’s not hard to measure spindle runout for a tool in the spindle: Total Runout: Which measures runout along an entire cylinder.įor the working machinist, it is perhaps more important to define run out as simply a measurement of the spindle runout of a tool (or workpiece) installed in the CNC Machine’s spindle directly.Circular Runout: Which measures runout only at certain specified circular cross-sections.Runout is so important to the design of rotating machinery that GD&T even has two kinds of runout: GD&T (Geometric Dimensioning and Tolerancing) is the science of defining and tolerancing allowable errors in manufacturing. We can create a run out definition very precisely using GD&T for specific situations. In other words, if you have a toolholder with 0.003″ of runout (that’s terrible, by the way!), and your endmill is only rated for 0.004″ of chip load, then you can only program a cut with 0.001″ of chip load (0.004 – 0.003) or you’ll exceed the cutter’s chip load limits.Īside from such catastrophic failures, runout is bad for tool wear in general. It’s a particular source of tool breakage for smaller cutters because runout is additive to chip load. It makes the tool wobble instead of spinning cleanly and increases chip loads. Runout is the tendency to spin the tool around a centerpoint that is not the tool’s center. It’s very bad for tool life, so it’s good to know more about it. Spindle Runout, or Tool Runout, as it can also be called, is the inaccuracies that cause a tool (in a mill) or workpiece (in a lathe) to spin off the ideal axis.
